Mitigating Risks and Maximising Efficiency with Flange Inspection Tags
Achieving safety compliance in industries that utilise flanges, such as oil and gas, is critical for preventing accidents and ensuring operational efficiency. One effective tool for enhancing safety compliance is the implementation of flange inspection tags.
Achieving safety compliance in industries that utilise flanges, such as oil and gas, is critical for preventing accidents and ensuring operational efficiency. One effective tool for enhancing safety compliance is the implementation of flange inspection tags. These tags not only facilitate record storage but also play a vital role in managing the risks associated with flange failures.
Flange Inspection Tags: Record Storage
Flange inspection tags are essential for maintaining accurate records of inspections and maintenance activities. According to safety regulations, records should be stored for up to three years if a flange has been broken.
This timeframe allows for thorough tracking of any issues and ensures that all necessary inspections and repairs are documented. Proper record-keeping can help identify patterns of failure and inform future maintenance strategies, ultimately enhancing safety and compliance.
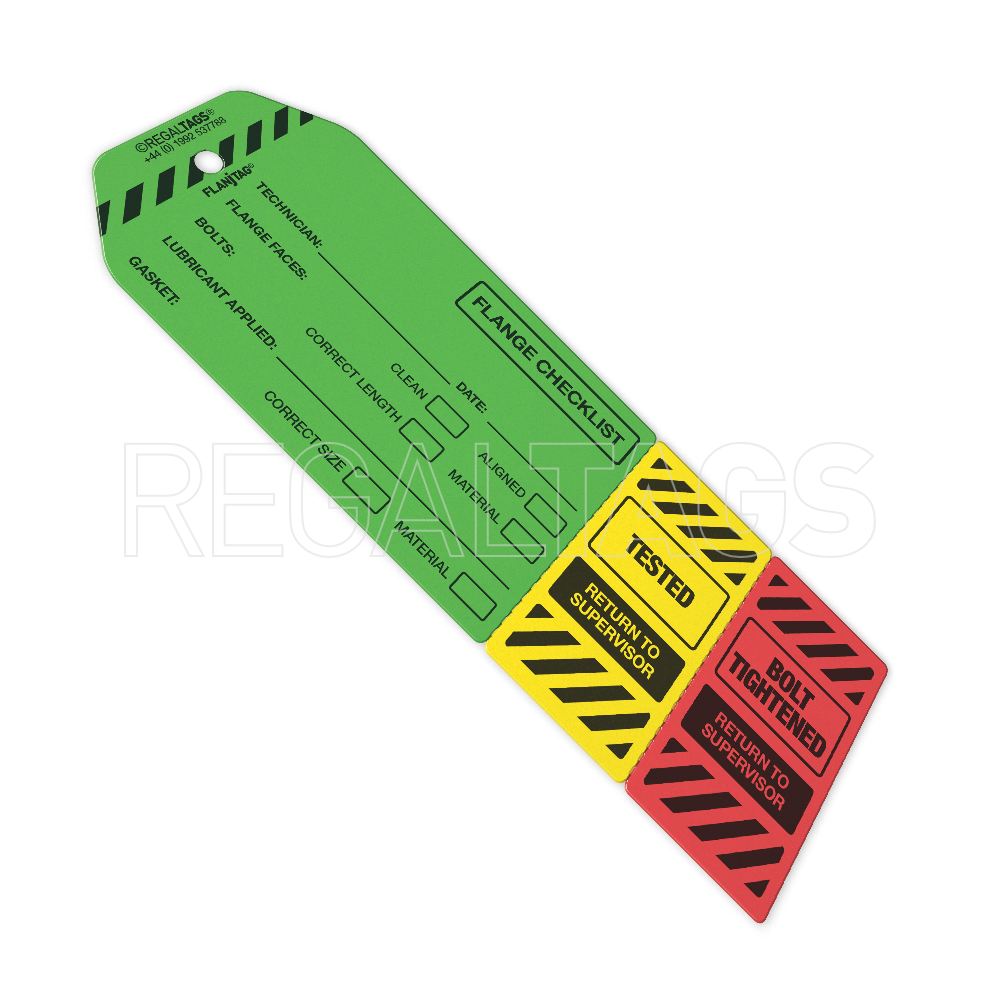
Consequences of Poor Flange Management
Neglecting proper flange management can lead to severe consequences, including:
- Leaks: Poorly managed flanges can result in leaks of hazardous materials, which can be particularly dangerous when transporting liquids or gases.
- Gas/Oil Leaks: These leaks pose significant risks not only to the environment but also to personnel safety. Gas or oil leaks can escalate quickly, leading to catastrophic incidents.
- Explosions: The potential for explosions due to flange failures is a serious concern, especially in high-pressure environments.
The implications of these failures can be dire, resulting in injuries, fatalities, and extensive damage to property and the environment.
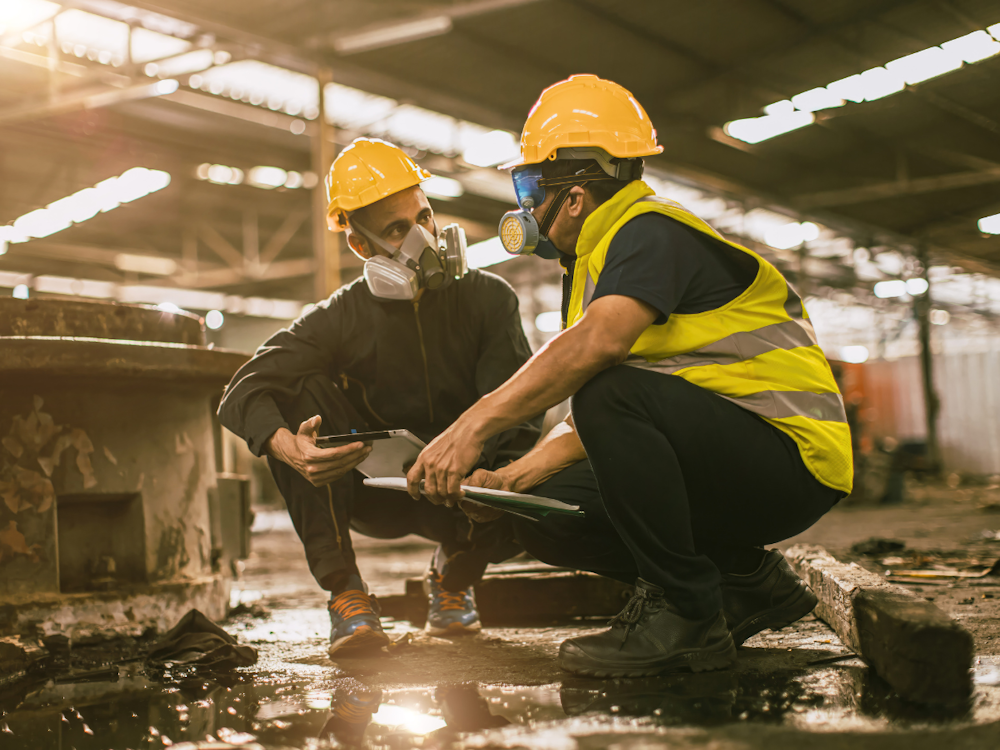
Financial Implications of Flange Failures
<pThe financial implications of flange failures can be significant, particularly in industries such as oil and gas where safety and operational efficiency are paramount. Here are some key statistics and insights regarding the costs associated with flange failures:
Cost of Downtime
The financial impact of downtime due to flange failures can be staggering. For instance, the cost of downtime for an oil rig can reach up to £100,000 per day. This figure highlights the critical need for effective flange management to prevent operational interruptions.
Pollution Costs
Flange failures can lead to leaks of hazardous materials, resulting in substantial costs for pollution clean-up and regulatory fines. The financial burden from environmental damage can escalate quickly, often reaching millions of pounds depending on the severity of the incident and the regulatory environment.
Insurance and Liability
Companies may face increased insurance premiums and liability costs following incidents related to flange failures. The financial repercussions extend beyond immediate repair costs, as companies must also manage the long-term impacts on their insurance coverage and reputation.
Corrosion Prevention Costs
The failure to implement effective corrosion prevention methods can lead to flange failures, which can incur costs in the range of £50,000 to £200,000 per incident, depending on the complexity and scale of the operation affected. Regular maintenance and inspections are essential to mitigate these risks.
Overall Financial Impact
A study indicated that flange-related failures contribute significantly to overall operational costs, with estimates suggesting that maintenance and repair costs could account for up to 15% of total operational expenses in some industries.
These statistics underscore the importance of proactive flange management and the implementation of effective inspection protocols to minimise the risk of failures and their associated financial impacts.
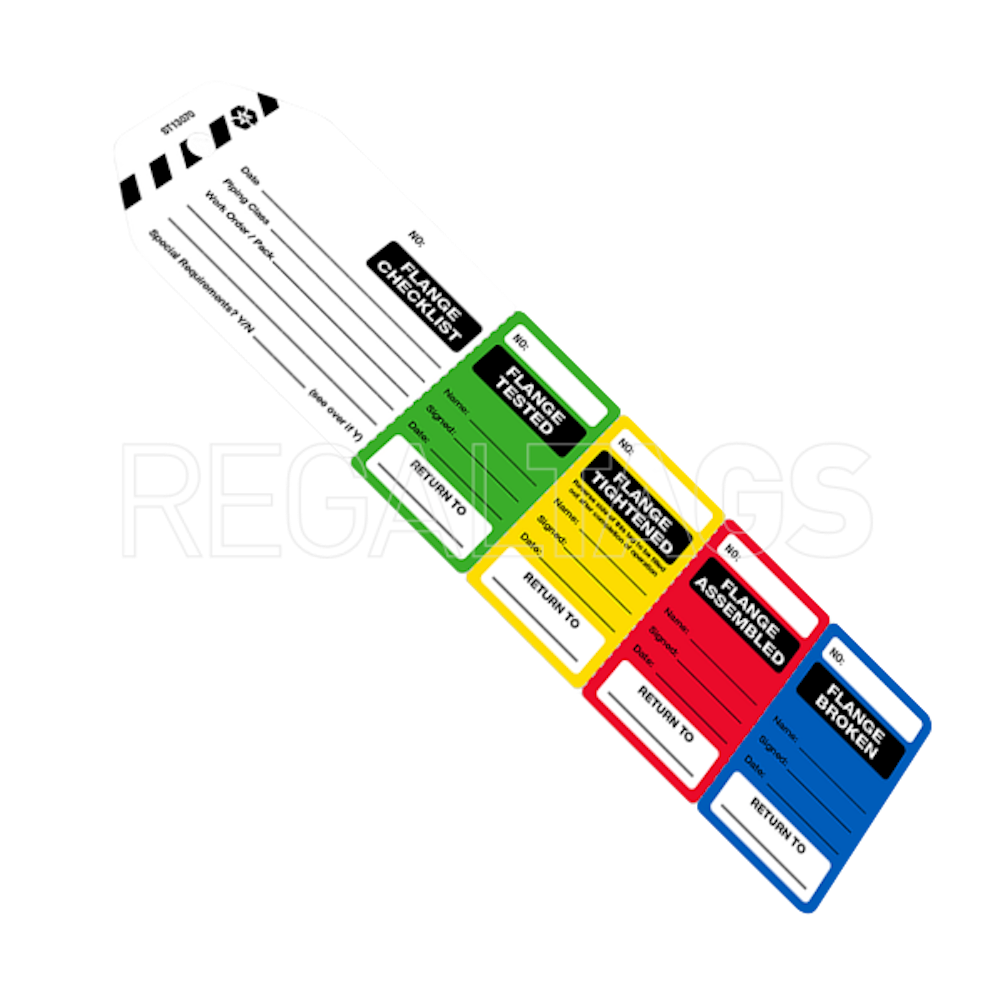
Material Considerations for Inspection Tags
The material used for flange inspection tags is crucial for ensuring durability and compliance. Tags must be resistant to various environmental factors such as moisture, UV light, and physical wear.
High-quality, weather-resistant, and tear-proof materials are essential to maintain the integrity of the tags over time. This reliability is vital for ensuring that the tags remain legible and functional, thereby supporting safety compliance efforts.
Contact us
We're just a call or click away.
Fill in the form below for direct contact with our team. We'll respond very shortly!
FLANGE INSPECTION TAGS FROM THE EXPERTS, REGALTAGS
Flange inspection tags are essntial tools for mitigating risks and maximising efficiency in industrial settings, particularly in the oil and gas sector.
By ensuring regular monitoring, early detection of potential issues, and accurate documentation, these tags play a pivotal role in preventing leaks and safeguarding both personnel and the environment.
If you’d like to find out more about how we can help with your inspection tags, contact our friendly team at REGALTAGS® today. We’re more than happy to answer any questions you have and can guide you through each material option.
Subscribe
Join 10,000+ others receiving our monthly updates. Free Tag knowledge delivered straight to your inbox.